August 15th 2023
How racers are simulating their way to success
As costs continue to rise and prying eyes aim to peek at any advantage they can see a rival working on, simulation is becoming an increasingly vital tool in motorsport. Its advantages for drivers — giving them near endless seat time ahead of events to learn tracks, cars, and procedures – are obvious, but simulation has a much wider use aside from letting people log laps.
NASCAR’s Next Gen car, now in its second season, was of course the product of countless real-world laps at a number of tracks, both on and off the Cup Series schedule. But while it was turning laps on track in late 2019 and early 2020, Landon Cassill was turning laps in the virtual world. Simulation has been a key component of NASCAR for over a decade now, with Cassill describing it as “absolutely fundamental.”
“The simulators are running all day, every day,” he tells RACER. “The only teams that aren’t using simulators at a large scale are the teams that aren’t factory backed or manufacturer supported. The largest teams like Hendrick, Joe Gibbs Racing, Stewart-Haas, those guys are probably in the simulator every single day. Maybe it’s not every driver every day and every team every day, but there’s probably some sort of team representation in that simulator seemingly every day.”
Such reliance on simulation is far from unique. Virtually — if you’ll pardon the pun — every series does it with track testing either outlawed or deemed too expensive to do on a regular basis.
“There’s been an evolution from on-track testing, which is really the best way to test a car but not necessarily the most efficient or cost-effective way,” says Cassill. “Racing series years ago put limitations around testing in an effort to control the costs that were spent on R&D, but if that money’s there, it’s going to get spent and smart people find a way to work around it, so that’s where simulation was created.
“But even before we were driving driver-in-loop simulators, the teams and manufacturers were building their cars and building their setups in simulation programs,” explains Cassill, who first tested with Chevrolet in the early 2010s. “Essentially (they were) preparing a virtual version of their race car and evaluating the potential data of that car before they ever put those setups underneath the real car. So NASCAR’s been pretty far along for a decade when it comes to engineering and simulation.”
It’s not all about cost-saving and efficiency, though. In series where regulations are tightly policed, simulation gives the opportunity to find sneaky advantages.
“In our sport, our cars are intended to look the same,” Cassill notes, “and so we don’t have the visual control of a wing of change or an underbody change that F1 has, where you can see those changes right in front of you and it’s easy to talk about. The teams have no choice but to talk about them or, or acknowledge them. As proprietary as the technology is, they can’t avoid it.
“In NASCAR — unfortunately for the sport, in my opinion, and for the fans — the teams are able to hide a lot of their technology around this stock body. And for years and years, there’s a lot of ingenuity that doesn’t get talked about because we don’t have to talk about it.”
The incognito nature of simulation also came in pretty handy for NASCAR’s recent foray at Le Mans. Before the Garage 56 project even got off the ground, Cassill may have — unknowingly, at the time — laid some of the groundwork while helping develop the Next Gen in its early days, as he divulged on Twitter back in June.
“I got a call from NASCAR — I’ve been in the sport for a long time and know a lot of the guys in the R&D center — and so got a call from them to come do a test, which to me wasn’t too unusual and I was happy to help with the Next Gen,” he explains. “They had a couple things that they were working through that I had known about, just being a full-time Cup driver at the time. I had known that they were testing and solving and developing that car to get it ready for us to race in the Cup Series.
“So nothing was too unusual for me, but they did ask me not to share much of the test plan when they sent it to me and showed me what we were doing — and the fact that we had Le Mans and the Daytona road course on the test plans. They had asked me to be prepared to run laps at Le Mans.”
For Le Mans, a baseline was needed. That was done with the help of iRacing laps in a Mercedes-AMG GT3 racer, and the previous generation of Cup Series car.
“It wasn’t super in-depth — it’s not like we were really turning big knobs, but they wanted to see a baseline of where we are at on this car at Le Mans. I wouldn’t say at the time that I had any specific knowledge or indication to myself that this was a potential Garage 56 entry and from that point on, I didn’t think much of it, to be honest with you.”
In fact, despite what NASCAR’s interest in Le Mans would develop into over the next three years, the simulator laps on Daytona’s road course drew Cassill’s attention more.
“I was, at the time, more interested in the fact that I ran laps on the Daytona road course as well because, being a current NASCAR driver, Le Mans seemed so far out there,” he says. “To me, I was more thinking, ‘Oh man, I’m probably going to end up racing at the Daytona road course’ and I hadn’t heard anybody talk about it. Obviously, that came into fruition pretty quickly because the Cup Series raced at the Daytona road course in short order after that.
“So the Le Mans thing wasn’t even really on my radar in the immediate future, other than I thought it was very exploratory. It didn’t feel random — I did feel like there was a purpose that NASCAR wanted to see some data of that car at Le Mans, how fast did it go down the straightaway and what the lap time looked like, the braking zones and what a general lap data would look like. So I knew there was a purpose. I just didn’t put too much thought into it like, ‘Oh, this thing might actually race.’
The on-track benefits of simulation to prepare cars and drivers might be relatively new, but the reasons for it are apparent. But now we’re also seeing engineers get their start in the virtual world as well.
“I’d say it’s happening a lot,” says Prescott Campell, an Oxford Brookes University student currently working as a structural engineer at the Williams F1 team, but who is also an engineer for Williams’ Esports division. “A lot of the other students I study with work part-time as engineers for various Esports teams, and they develop these skills that you don’t really learn during university — how to set up a race strategy, that’s not really a course that’s taught.
“So they can build these skills by being engineers for Esports teams and the software that’s used to analyze data is the exact same software that’s used in real life, so you get familiar with software that they need to use to get a job after graduating.”
The idea of an “engineer” in a virtual world might seem baffling at first but, as with driver and car prep, the reasons behind it are straightforward.
The idea of an “engineer” in a virtual world might seem baffling at first but, as with driver and car prep, the reasons behind it are straightforward.
“With anything that’s extremely competitive, you need as many tools and people on the case as possible to efficiently find every advantage you can,” says Campbell. “It’s possible, but it requires a lot of work for a driver to converge on setups and they might not have the skills to use the software and the tools available in order to exploit these advantages that they might never come across.
“So it takes an engineer that has experience with data analysis and the tools they need to extract data from the driver running, then sweep through it, working with the driver — who might also pick up things that the engineer might not notice — and then try different things when the driver’s complaining about something or saying the car can be improved in a certain way.
“It’s the engineer’s expertise that can tell them what sort of setup change and direction they can go in. That’s not something the driver might know unless they have so much experience with setup changes.”
The virtual world also gives engineers — either working exclusively in the virtual world, or preparing for the real world — more time and space to figure out solutions.
“In real life, often the engineer has to make informed decisions on what not to look into, and to decide just based on their own experience, different aspects of the car to ignore or keep the same while they try and converge on a precise setting on a different aspect of the car,” Campbell says. “While in sim racing, you can basically sweep through all of these things because you have as much time as the drivers are willing to spend online.”
That being said, for drivers, the idea of “just pressing the reset button” feels like less of a luxury.
“Even just the process of resetting the lap if you make a mistake or crash still takes time — the time it takes to reset, but also the time it takes to start that lap over,” explains Cassill. “If you’re doing that, not even on a warmup, on a run change that you make in the car so that they can compare the data after the fact, you’re trying to get a clean lap for every single change.
“If you keep making mistakes or if you keep crashing, you’re kind of muddying up the data and resetting and that time compounds on itself. Just like any line of work — racing isn’t really that special when you’re trying to think of time over productivity, right? Just like anything, you get to the end of your shift and you’re like, ‘Man, have two more runs to get through — where did we lose that time?’ So I always try to be as efficient as possible in my feedback and how I get up to speed.
“To me it’s very similar to the final hour of a practice session. It’s like a two-minute drill for a quarterback. I try to approach the sim sessions as seriously as I would a practice session and be as efficient and diligent as possible.”
Because saving time, ultimately, is what results on the racetrack are all about.
For more information: www.racer.com
For more information: www.racer.com
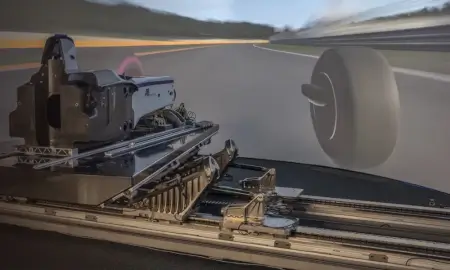